Quality Improvement Kaizen Event in the Pharmaceutical Sector
PROJECT TITLE:
Quality Improvement Kaizen Event
KEY BUSINESS CHALLENGES AND PROJECT OBJECTIVES:
Our Pharmaceutical client processes batches in a continuous process, with the specifications of one critical feature between 2 and 5%. It was noted that at the start of the 2018 that the product was performing towards the lower specifications. As a result, approximately 50% of the product was reworked. Given the implications of operating at a lower specification, a cross functional Kaizen team was assembled with the following objectives
- Increase product average to 3.5% +/- 0.1
- Eliminate non-value-added rework activities
CLS APPROACH AND CHANGES IMPLEMENTED:
CLS worked with the Project Team, identifying containment actions that would contain the processing of lower specification product, with the implementation of additional testing.
Next, an SPC analysis of the baseline information was performed, which identified when the process shifted in average. From an analysis of change controls, the root cause of the problem was identified, and actions were implemented to counteract the root cause including changes in pumps, pipework and valves. The Kaizen team walked the process, from tank to tank, and identified other process steps that may have contributed to the problem. 10 Areas were identified and prioritised by the team, which resulted in 4 key projects being identified and agreed by the entire team.
These projects were reviewed monthly and over the course of 4 months, key changes were implemented through the change control process including changes to Product Unit design, modification to the management of flow of product, changes in temperatures and heat exchanger modifications.
As a result of the changes implemented, the additional measurements were reduced, and the process is now monitored on an SPC chart real time.
RESULTS / OUTCOMES: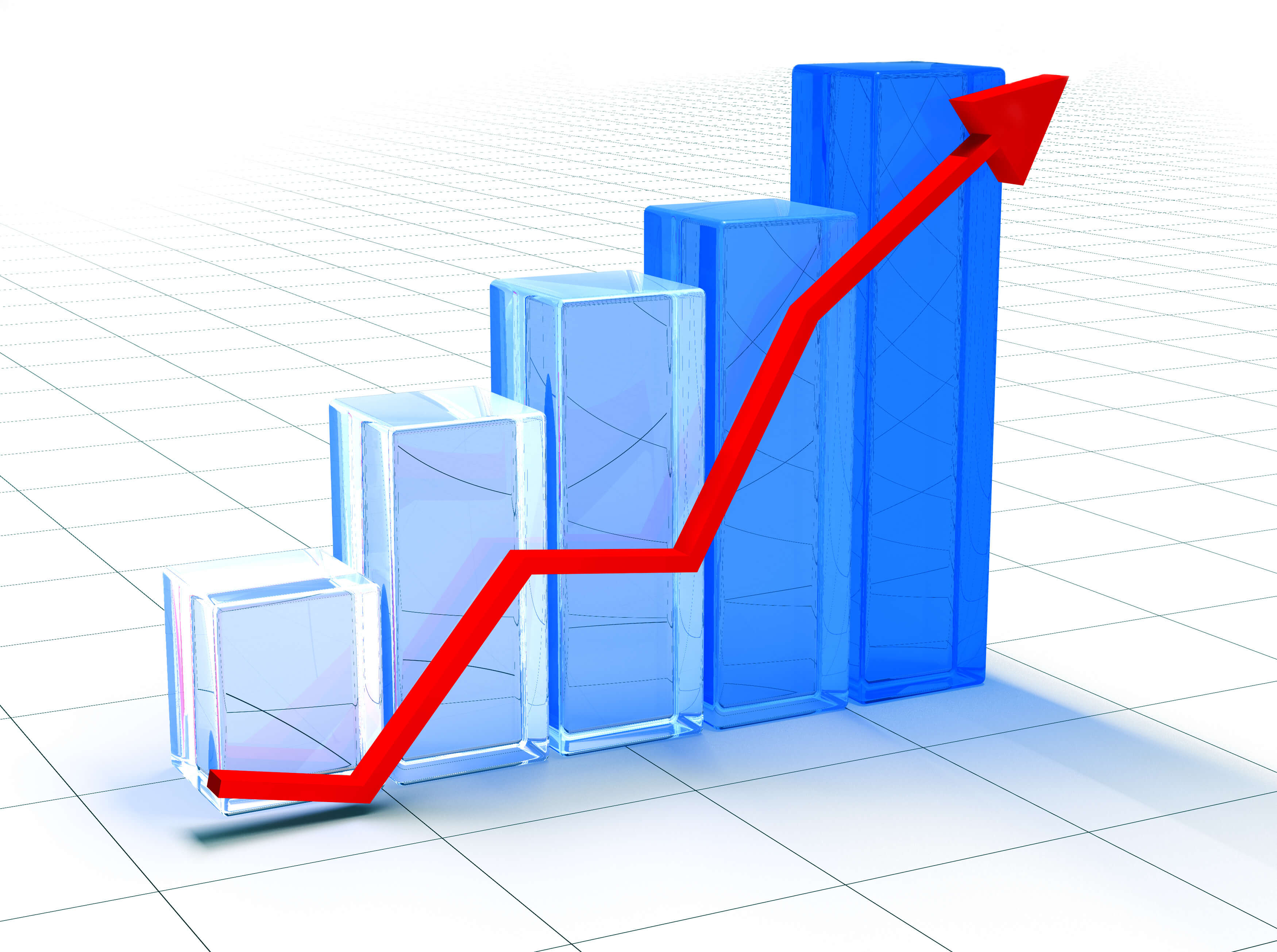
- The process average increased from 2.7% to 3.6%, with the SPC chart highlighting no special causes
- Reduced variability compared to baseline data
- Reduced rework time by 90%
- Full engagement of the team ensured an optimal result to a problem that could not be addressed by one person alone. The quality of the final solutions was dependent on the knowledge of the entire value stream which was a critical success factor in the identification of a sustainable solutions.
CONTACT US:
To find out more about using a Kaizen based approach for process improvement, contact maria.ryan@crystalleansolutions.ie