Systematic Approach to Problem Solving delivers time and cost benefits
Working with a client in reverse was an interesting experience for Managing Director Maria Ryan when she interviewed Modular Automation’s principal applications engineer Colm O’Connor in a recent Mid-West Lean network event.
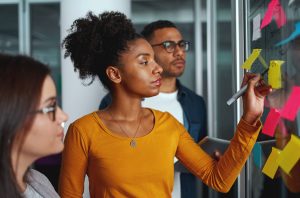
Problem solving was the topic for discussion at the webinar and, having worked with Colm and his team on a problem solving project, Maria was very familiar with the outcomes that could be derived from introducing rapid problem solving (RPS) in a company. It was interesting to move from the consultant’s chair to that of the interviewer and select a set of questions that would enlighten the audience and encourage them to review their in-company problem solving methodologies.
As Maria explains: “When designing the interview, the first time this type of approach was taken to communicate a lean process at a Mid-West Lean Network series, I considered it from the context of: What would I want to hear if I was attending the webinar and how would I like the information presented and what are the key messages that we communicate to clients when deploying problem solving?
During the interview Colm O’ Connor outlined how finding the direct cause of any problem is the easy part; identifying its root cause is more difficult but that is where the quality of the solution lies and where cost and time savings are gained. Putting a structure in place to arrive at this state is so important; sporadic approaches to problem solving will, in the long term, affect the quality of the solution and that’s where the extra costs come into play.

Key Steps for Deployment:
- Align program to strategy and assign a Sponsor and team to lead into an organisation
- Analyse the various problem solving tools available – there are many, for example A3, Rapid Problem Solving (RPS), Toyota method for A3, the Scamper technique, Six Hats. You can do this with your continuous improvement team or in conjunction with your lean consultant.
- Plan how you are going to get people to use the tool and how you will get buy-in company-wide. If the problems you encounter are cross-departmental, as was the case with Modular Automation, then make sure you train people across departments to use the tool. Roll-out and implementation is critical.
- Identify core people across departments as champions and as mentors and, most importantly, select influential people in the company to drive it. If some of the problems you encounter involve sub-suppliers, get them on board too as the problem may recur if it is linked to how you are using a component, which, in Modular Automation’s case was the root case of a problem. Once detected, this can then be documented and used for future reference.
- Select Pilot, train staff and complete lessons learned.
- Gain consistency though getting people to use the tool.
- Encourage leadership to coach and mentor as part of the company culture.
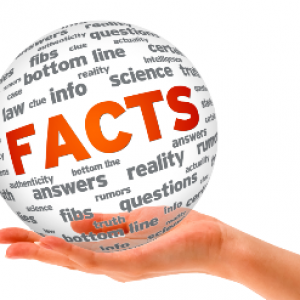
Modular Case Study
Modular Automation overcame initial pain points and now have a structure thought process in place for solving problems, records for reference purposes, and people and mentors in all departments trained to use RPS. With customer central to lean thinking, this also gives their customers confidence.
The Company’s 6-step process for problem solving involves:
- Defining the problem
- Determining the root cause
- Generating alternative solutions
- Selecting a solution
- Implementing the solution
- Evaluating the outcome
Key Take Aways:
Key takeaways on RPS from this Mid-West Lean Network event included:
- Analyse the options available for solving problems at the level your company requires.
- Choose what suits your business best.
- Spend time brainstorming.
- Attain consistency though getting people used to working with the tools.
- Select influential people in the company to drive the change.
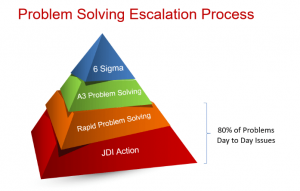
If your company would like to adopt a unified approach to problem solving, our team would be delighted to assist you.
Also, check out Enterprise Ireland’s or your Local Enterprise Office’s websites for details of funding available to support your lean journey.
Useful Links