Our Learnings from The Enterprise Excellence Conference
Crystal Lean Solutions recently attended and exhibited at the Enterprise Excellence Conference in May 2019 and have put together a blog to share their key learning points from the day.
Opening of the Enterprise Excellence Conference
The Enterprise Excellence Conference was opened by Minister Sean Canning TD and a number of keynote speakers, including Mary Buckley from the IDA and Enterprise Ireland provided valuable insights into the value of Lean Deployment in enabling Competitiveness and Productivity.
As Crystal Lean Solutions attended a number of different presentations on the day (very similar to their WIT blog which proved to be popular) they have decided to do the same with their day at the Enterprise Excellence Conference. So if you missed a presentation or you were unable to attend continue reading and hopefully you will get something out of this blog.
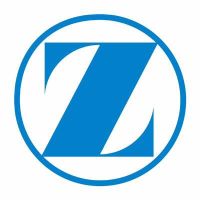
Company: Zimmer Biomet
Presenter: Adrian Furey
Title: VP Global Supply Chain & Logistics
Overview & Key Learnings:
Adrian presented his 3 year journey transforming the site in the US to a highly engaged safety and quality conscious culture.
Key learnings from his journey included:
- Help people to really “see” the process. Here he noted each day a door with a safety issue and observed how many people walked past this every day. He started small and simple and focused on this first safety observation
- Communicate with your organisation – establish a communication process to connect with your organisation. Here Adrian provided people with his e-mail address directly to facilitate access to him across the organisation
- Empower your employees – provide employee opportunities to improve, both their own areas and their own careers
- Leadership is critical to effective change
- Focus on improving value to employees – create a workplace that you are proud to work in
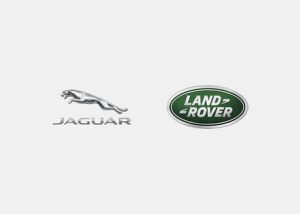
Company: Jaguar Land Rover
Presenter: Dr. Heiko Gierhardt
Title: Global Director launch in Purchasing
Stream: Transformation in Services
Overview & Key Learnings:
Dr. Heiko Gierhardt was recently appointed with the title Global Director Launch in Purchasing with Jaguar Land Rover. He provided an overview of his launch and Crystal Lean Solutions have put together some of his key learnings from it.
Key Learnings:
With reference to a full business transformation Dr. Gierhardt recommended understanding each system and then improving by the following;
- Knowing 4 to 5 employees of each plant so they will be your voice and ears of the place
- Change rather than talking about change
- Select one risk assessment project
- Management of Risks; if something is late, what is it and why is it late, when is it due
- Set up a Governance process team – track to solution, make decision
- Management of Suppliers – one way to supplier from the plant
- Single source of truth – one report managing the full transformation including risks
Soft Points
- People & Leadership
- Important Strategy
- Trust and Respect
Dr. Heiko Gierhardt leads from the front and by tasks, trying to be with suppliers and transformation hot topics so he has an understanding of the system. He is a strong advocate of learning from failures.
At the end of his uplifting talk he advised that if it doesn’t work, keep calm and patient.
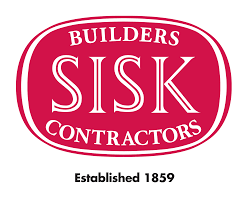
Company: John SISK and Sons Ltd
Presenter: Joe O’Sullivan and Cormac
Title: Lean in Construction
Overview & Key Learnings:
SISK very cleverly utilised the 5 Lean principles when building Centre Parcs in Longford. Outlined below are some of the steps taken resulting in what SISK describe as their best project to date “To build a State of the Art Own in 400 acres of Woodland in less than 70 weeks.
- Identify value from the customers perspective including Regulatory, Client, SISK and Sub Contractors perspective
- Identify the steps in the value stream
- Establish Pull and Flow using interactive planning, on-boarding of subcontractors and allowing gaps in the schedule between trades
- Use of offsite construction resulting in output of 20 units/week against an industry norm of 4 units per week
- Use of standardisation for the installation of complex chimney installations
- Standardisation of Material management – kitting for each house
- Application of digital project delivery to support visualisation of the project for all sub-contractors
- Use of Visual Communication to support meeting the plan daily
Company: Thermoking
Presenter: Cormac Mac Donncha
Title: Operations Director
Stream: Transformation to Manufacturing 4.0
Overview and Key Learnings:
After Cormacs introductions he presented Thermoking Lean Journey in Video format.
Thermoking have been on their Lean Journey for 20 years. At the start of there journey they saw breakthrough improvements and after 20 years it is now in an incremental improvement phase.
They are 11 years without a lost time accident and have 81% of employee engagement. Thermoking use Gemba on the factory floor and A3, 9 step basic problem solving. Using real time data, they can save data and review when they wish.
Thermoking went robotic, this helps prevents straining and other injuries. Cormac also mentioned since going Robotic it also prevents error as they used to hand write everything.
The company brought in a box style forklift but to have this style it meant they had to change the layout of the factory. As a result of the box style forklift, maintenance costs were reduced including batteries etc.
1 robot reduces the requirement from 7 employee to 1 for their process. Subsequently they up-skilled a number of their employees.
Cormac pointed out at the end of the video clip that we would have noticed that everyone in the video was male, there industry is exclusively male. Cormac put an open invitation out for female employees to engage with Thermoking.
If you want to recap or have your first read of our WIT Learnings, click on the link below.
Our Learnings From The 7th Annual WIT Enterprise Excellence Forum
Crystal Lean Solutions – “Delivering Excellence Together”